Piping
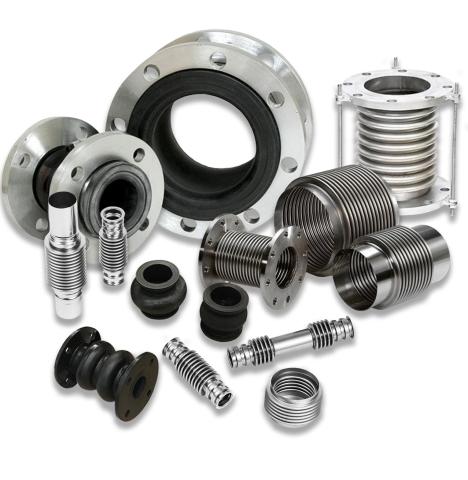
Piping expansion joints, also known as compensators or expansion bellows, are flexible components installed in piping systems to absorb thermal expansion, vibration, and movement while maintaining the integrity of the system. These joints are particularly crucial in systems where pipes are subject to fluctuations in temperature or pressure.
Expansion joints are typically composed of flexible materials such as rubber, metal, or a combination of both. They are designed to allow controlled movement in multiple directions, including axial (lengthwise), lateral (sideways), and angular movements. This flexibility helps to prevent stress, strain, and damage to the piping system and its components.
Expansion joints are commonly used in various industries, including HVAC, power generation plants, petrochemical and chemical processing plants, oil and gas pipelines, marine and shipbuilding applications, water and wastewater treatments, and pharmaceutical and food processing industries.
At Macroseal, every expansion joint we manufacture is a tailored solution to a specific problem. Our team excels in identifying the unique challenges of each situation and recommending the most effective expansion joint, whether it's a standard option or a custom-made design. For instance, when dealing with misaligned and at angle pipes or ducts, a standard expansion joint often falls short. It requires multiple adjustments, compromising efficiency and lifespan. In such cases, a custom expansion joint is essential. Unlike a standard joint, which loses several life cycles through frequent adjustments and strain, a custom-made joint fits perfectly from the start, ensuring optimal performance and longevity.
Understanding the different types of arches, reducers, and motions that expansion joints accommodate, is also crucial for selecting the appropriate joint for specific applications, for example:
Piping Expansion Joint Motions:
Axial movement: For applications involving face-to-face movement, axial expansion joints are ideal as they can compress or extend to adapt to changes in pipe length. We categorize these into two types: axial compression, which decreases the joint's length along its longitudinal axis, and axial elongation, which increases the joint's length along the same axis. Bellows, flexible rubber sections, or telescoping mechanisms are commonly used to accommodate this movement. We typically utilize these expansion joints in situations where temperature fluctuations lead to thermal expansion or contraction of the pipe length, where these joints effectively manage the thermal stresses.
Lateral or transverse movement: For applications requiring side-to-side movement, lateral expansion joints are optimal as they allow the displacement of the joint's ends in a direction perpendicular to its longitudinal axis. This movement is accommodated by flexible elements capable of bending and stretching while maintaining the joint's integrity. We frequently employ lateral expansion joints to accommodate ground shifts or structural movements, particularly in situations where ground settlement causes horizontal shifts in the pipeline.
Vibration: In piping systems, vibration movement is critical to the design and operation process. It refers to the ability of expansion joints to absorb or dampen mechanical oscillations caused by dynamic factors like equipment operation, fluid flow turbulence, or external influences such as machinery vibration. Proper management of vibration movement is essential to prevent damage to the piping system, reduce noise, and ensure longevity and reliability. Effectively controlling these mechanical oscillations allows the system to operate smoothly, safely, and efficiently, enhancing its overall durability and performance.
Angular movement: For applications involving rotation around the pipe or joint centerline, angular expansion joints are ideal as they accommodate deviations from the expansion joint's initial straight-line position, these movements are measured in degrees. This angular displacement results from a combination of axial elongation and compression. Hinged mechanisms or flexible materials that allow for angular movement are typically used. We commonly utilize angular expansion joints in scenarios where we expect pipeline bending, these joints play a crucial role in absorbing those bending forces when subjected to external factors like wind, dynamic loads, or seismic activity, for instance.
Torsional movement: For applications that involve twisting of the pipe around its axis, rotational expansion joints are ideal. They accommodate the rotational displacement of one end of the joint relative to the other around its longitudinal axis, these movements are measured in degrees. Torsional joints typically utilize materials and designs that can endure rotational stress without permanent deformation. We employ these joints in scenarios where pipelines experience misalignment or rotational forces. They effectively manage twisting stresses in rotating machinery connections or pipelines subjected to torsional forces.
Concurrent movement: The combination of two or more of the above expansion joint movements, which can also be referred to as the "Resultant Movement". The formula for calculating the concurrent movement is: Concurrent movement = Compression + Elongation + Lateral + Torsional. Angular movement is not separately added because it is inherently covered by compression and elongation when considering concurrent movements. Therefore, ensure that the sum of Compression, Elongation, Lateral, and Torsional movements does not exceed "1". If it does, the joint may be operating outside its design intent and should be evaluated. We typically employ these joints in complex situations where both thermal expansion and seismic activity impact the pipeline. They are crucial for providing flexibility in intricate piping networks or areas with multi-directional movement. Designed to accommodate multiple types of movement simultaneously, these joints often incorporate various flexible elements or sections to effectively manage complex motion patterns.
Types of Piping Expansion Joint Reducers:
Expansion joint reducers are commonly constructed from materials like rubber, elastomers, stainless steel, or other alloys, these joints are tailored to the specific application requirements to ensure durability and performance. They provide essential flexibility to absorb thermal expansion, seismic movements, or structural shifts without compromising the integrity of the piping system, thereby maintaining smooth operation and longevity. Here are the primary types of piping expansion joint reducers:
Concentric Taper: Also known as a concentric reducer expansion joint, is a specialized type of expansion joint that we use in piping systems to accommodate changes in pipe diameter while absorbing movement, vibrations, thermal expansions, and other dynamic forces and maintaining the integrity of the piping system. It is structured with two ends that smoothly transition between different pipe diameters along the same centerline. Its conical or tapered shape starts with a larger diameter at one end and gradually reduces to a smaller diameter at the other. When connecting piping sections with different diameters, concentric expansion joints ensure a seamless integration in a concentric manner, preventing abrupt changes that could compromise system performance.
Eccentric Taper: Also known as an eccentric reducer expansion joint, we often used it where changes in pipe diameter and movement absorption are necessary to accommodate motion while preserving structural integrity and maintaining flow continuity within the piping system. Similarly, it is structured with two ends that transition between different pipe diameters, but it differs from its concentric counterpart in structure and functionality, unlike concentric joints, the transition is offset from the centerline. Its conical or tapered shape starts with a larger diameter at one end that gradually reduces to a smaller diameter at the other end. When connecting piping sections with different diameters, eccentric expansion joints ensure a transition that is not centered, which proves beneficial in specific piping configurations where centered transitions are not feasible or desirable.
Angular Offset: An angular offset expansion joint is designed to accommodate angular movements in piping systems or offset between two connected piping sections. They consist of flexible components that allow for bi-directional movement, typically using hinged or gimbal designs. The design incorporates hinge plates or gimbal rings, enabling rotational movement around the joint's longitudinal axis, measured in degrees.
Lateral Offset: A lateral offset piping expansion joint is designed to accommodate lateral movements or offsets between two connected piping sections. They typically consist of flexible components such as bellows or corrugated elements that enable lateral displacement. Depending on the required movement capacity, the design can include single or multiple bellows to accommodate various degrees of lateral movement.
Angular/Lateral Offset: An angular/lateral offset piping expansion joint is specifically engineered to manage angular displacement or offset between two interconnected piping sections. Structurally, it comprises flexible components that facilitate movement in two planes (bi-directional), often incorporating hinged or gimbal designs. These designs typically feature hinge plates or gimbal rings that allow rotational movement, measured in degrees, around the longitudinal axis of the joint.